재질개량 침엽수 간벌 소경재를 이용한 목제욕조 제조기술에 관한 연구
Studies on the manufacturing Technique of wooden-bathtub made with thinned modified softwood
- 한국가구학회
- 한국가구학회지
- 한국가구학회지 제8권 제1호
-
1997.1247 - 56 (10 pages)
- 0
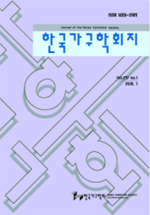
This study was carried out to develop the manufacturing techniques of new wooden bathtub and wooden tile to utilize thinned softwoods for bathroom. The manufacturing process of wooden bathtub was composed of 8 stages; (1) sawing and drying, (2) lamina cutting, (3) laminated assembly, (4) joint processing, (5) treated with preservatives, (6) bathtub assembly, (7) treated with urethan -resin, (8) treated with fluoro-resin. Isocyanate adhesives(KR-120) showed good bonding propeties in water proofing, warm-water proofing, and boil proofing test. Wooden bathtubs treated with urethan-resin and fluoro-resin were free from any defects by KS F 2826. Especially, wooden bathtub treated with Huoro-resin showed excellent properties in hot-water resistance, boil proofing, accelerated weathering than those of urethan resin. But in abrasion resistance and washing resistance, treatments with urethan-resin were more superior than those of Huoro-resin. So, it is considered to be desired that urethan-resin was applied at the first and second coat and Huoro-resin was applied the final coat. The manufacturing cost of a wooden bathtub made with thinned softwood was counted about 184,057won and this cost comes under one tenth of Japanese wooden bathtub made with Chamaecyparis obtusa.
1. 서론
2. 재료 및 방법
3. 결과 및 고찰
4. 결론
5. 참고문헌
(0)
(0)