Simulation of Ultrasonic Stress During Impact Phase in Wire Bonding
- 한국마이크로전자및패키징학회
- 마이크로전자 및 패키징학회지
- 제20권 제4호
-
2013.127 - 11 (5 pages)
-
DOI : 10.6117/kmeps.2013.20.4.007
- 0
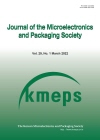
As thermosonic ball bonding is developed for more and more advanced applications in the electronic packaging industry, the control of process stresses induced on the integrated circuits becomes more important. If Cu bonding wire is used instead of Au wire, larger ultrasonic levels are common during bonding. For advanced microchips the use of Cu based wire is risky because the ultrasonic stresses can cause chip damage. This risk needs to be managed by e.g. the use of ultrasound during the impact stage of the ball on the pad ("pre-bleed") as it can reduce the strain hardening effect, which leads to a softer deformed ball that can be bonded with less ultrasound. To find the best profiles of ultrasound during impact, a numerical model is reported for ultrasonic bonding with capillary dynamics combined with a geometrical model describing ball deformation based on volume conservation and stress balance. This leads to an efficient procedure of ball bond modelling bypassing plasticity and contact pairs. The ultrasonic force and average stress at the bond zone are extracted from the numerical experiments for a 50μm diameter free air ball deformed by a capillary with a hole diameter of 35μm at the tip, a chamfer diameter of 51μm, a chamfer angle of 90°, and a face angle of 1°. An upper limit of the ultrasonic amplitude during impact is derived below which the ultrasonic shear stress at the interface is not higher than 120 MPa, which can be recommended for low stress bonding.
1. Introduction
2. Geometric Model of Ball Deformation
3. Ultrasonic Finite Element Model
4. Conclusions
Acknowledgement
References
(0)
(0)